1. Concept Overview
1.1. Saucer Module with Arms:
1.2. Modular Starship Integration:
2. Potential Advantages
2.1. Scalable Propulsion and Mission Flexibility:
2.2 Redundancy and Safety:
2.3. Operational Versatility:
2.4. Technological Advancement:
3. Engineering and Technical Considerations
3.1. Structural Integrity:
3.1.1. Saucer Construction:
3.1.2. Docking Arms:
4. Docking and Attachment Systems:
4.1 Universal Docking Ports:
4.2 Automated Docking Procedures:
5. Propulsion Coordination:
5.1. Thrust Vectoring:
5.1.2. Fuel Management:
6. Systems Integration:
6.1. Power Distribution:
6.2. Life Support:
7. Control and Navigation:
7.1. Unified Command Interface:
7.2. Attitude Control:
8. Safety Protocols:
8.1. Emergency Detachment:
8.2. Redundant Systems:
9. Challenges and Solutions
9.1. Aerodynamics During Launch:
9.2. Mass and Fuel Efficiency:
9.3. Technological Feasibility:
9.4. Structural Complexity:
10. Potential Applications
10.1 Deep Space Exploration:
10.2 Space Stations and Habitats:
10.3. Scientific Research:
10.4. Tactical and Emergency Operations:
11. Limitations for Interstellar Travel
-
Propulsion Upgrades: As propulsion technology advances, the saucer module could integrate newer systems, such as fusion or ion engines, to extend its operational range.
-
AI-Guided Research: Utilizing AI to monitor and predict potential upgrades, such as emerging propulsion technologies, will keep the spacecraft adaptable and future-ready.
-
Interstellar Module Integration: Consider designing a dedicated module that could replace the Starship engines with interstellar-capable propulsion systems when they become available, thus preserving the saucer module for multi-generational missions.
12. Generating Artificial Gravity in the Saucer Section
12.1. Importance of Artificial Gravity
12.2. Methods for Generating Artificial Gravity
12.2.1. Spinning the Entire Saucer Section
-
Advantages: Uniform Gravity: Provides consistent artificial gravity throughout the main habitat. Simplified Interior Design: Eliminates the need for transitions between gravity and zero-gravity areas within the saucer.
-
Challenges: Gyroscopic Effects: Rotating a large mass introduces significant gyroscopic torques, complicating attitude control and maneuverability. Docking Complexity: Makes docking with other spacecraft more challenging due to the saucer’s rotation. Mechanical Stress: Requires robust systems to handle the structural stresses from continuous rotation.
12.2.2. Incorporating Rotating Habitat Rings within the Saucer
-
Advantages: Localized Gravity: Provides artificial gravity in specific areas without rotating the entire saucer. Reduced Gyroscopic Impact: Smaller rotating masses have less effect on the spacecraft’s overall maneuverability.
-
Challenges: Mechanical Interfaces: Requires reliable bearings and seals between rotating and stationary sections. Complex Layout: Designing efficient transitions between gravity and zero-gravity zones can be intricate.
12.2.3. Redesigning as a Spinning Sphere
-
Advantages: Structural Efficiency: A sphere can handle rotational forces effectively due to even stress distribution. Uniform Gravity: If the entire sphere rotates, it provides consistent artificial gravity.
-
Challenges: Design Overhaul: Alters the iconic saucer design, impacting the vessel’s aesthetic and internal arrangement. Mechanical Complexity: Similar gyroscopic and mechanical issues as spinning the saucer.
12.2.4. Adding External Rotating Rings to the Saucer
-
Advantages: Modularity: External rings can be added or removed based on mission needs. Simplified Main Structure: Keeps the central saucer stationary, simplifying critical systems.
-
Challenges: Structural Support: Requires strong support structures, increasing mass and complexity. Exposure Risks: External rings are more susceptible to radiation and micrometeorite impacts.
12.3. Recommended Solution: Incorporating Rotating Habitat Rings
12.3.1. Design Integration
-
Placement: Attach one or more rotating rings around the saucer’s perimeter, maintaining the vessel’s iconic profile while adding functional enhancements.
-
Counter-Rotation: Utilize counter-rotating rings to balance angular momentum, minimizing net gyroscopic effects on the spacecraft’s orientation.
-
Structural Supports: Employ lightweight, high-strength materials for support structures housing magnetic bearings and superconducting systems to enable smooth rotation.
12.3.2. Mechanical Systems
-
Rotation Mechanisms: Use magnetic or superconducting bearings to minimize friction and wear, enhancing reliability and reducing maintenance needs.
-
Environmental Seals: Implement advanced sealing technologies to maintain atmospheric integrity between rotating and stationary sections, ensuring crew safety and comfort.
-
Power and Data Transfer: Utilize wireless power transmission (inductive coupling) and communication systems to connect the rotating habitats with the main spacecraft systems seamlessly.
12.3.3. Human Factors
-
Gravity Levels: Adjust rotation speed and ring radius to create artificial gravity levels appropriate for human health, such as Earth-like gravity (1g) or partial gravity for adaptation.
-
Habitat Design: Design the interior spaces of the rings to maximize comfort and functionality, including living quarters, dining areas, exercise facilities, and recreational spaces.
-
Transition Areas: Create vestibules or transitional corridors that help crew members acclimate when moving between zero-gravity and artificial gravity environments, reducing disorientation.
12.3.4. Advantages of the Rotating Habitat Rings
-
Minimal Impact on Maneuverability: The main spacecraft remains stationary, preserving its maneuverability and simplifying navigation and docking procedures.
-
Design Flexibility: Rings can be added, removed, or reconfigured based on specific mission requirements and crew size, enhancing the spacecraft’s versatility.
-
Maintenance and Upgradability: Individual rings can be serviced, repaired, or upgraded without impacting the entire spacecraft, extending the vessel’s operational lifespan.
12.4. Addressing Challenges
12.4.1. Mechanical Complexity
-
Redundancy: Incorporate redundant systems and components to ensure continuous operation in case of mechanical failures, enhancing overall reliability.
-
Monitoring Systems: Use advanced sensors and AI-driven diagnostics to monitor the mechanical health of rotating components in real-time, enabling predictive maintenance.
12.4.2. Structural Integrity
-
Simulation and Testing: Conduct rigorous simulations, such as finite element analysis (FEA), to predict stresses and deformations, informing design optimizations.
-
Material Selection: Utilize advanced materials with high strength-to-weight ratios and fatigue resistance to withstand the stresses of continuous rotation.
12.4.3. Safety Protocols
-
Emergency Stop Mechanisms: Implement systems capable of safely decelerating and stopping the rotation in case of emergencies, preventing harm to the crew and the spacecraft.
-
Autonomous Safety Systems: Equip rotating habitats with fire detection, suppression systems, and automatic sealing capabilities to isolate sections if necessary.
-
Evacuation Procedures: Develop clear protocols for the safe evacuation of crew members from rotating habitats in the event of mechanical failures or other emergencies.
12.5. Alternative Solutions
12.5.1. Short-Arm Centrifuges
-
Usage: Install centrifuge-equipped modules or facilities where crew members can spend time periodically to mitigate the effects of microgravity.
-
Benefits: Provides artificial gravity exposure without rotating large sections of the spacecraft, reducing mechanical complexity.
12.5.2. Artificial Gravity via Linear Acceleration
-
Method: Employ constant acceleration or deceleration of the spacecraft to simulate gravity during certain mission phases.
-
Limitations: Not practical for missions requiring stationary periods or precise orbital mechanics, and provides gravity only during acceleration phases.
12.5.3. Pharmacological Countermeasures and Exercise Regimens
-
Approach: Rely on medical interventions, such as medications and rigorous exercise programs, to mitigate the adverse effects of prolonged weightlessness.
-
Limitations: May not fully prevent long-term health issues associated with microgravity and requires significant time commitment from the crew.
13. Advancements and Innovations:
-
Modular Architecture: Enhances flexibility, allowing the spacecraft to evolve with mission needs and technological advancements.
-
AI-Driven Operations: Incorporates cutting-edge AI for docking, navigation, and systems management, increasing efficiency and safety.
-
Collaborative Potential: Opens opportunities for international cooperation, with standardized docking systems enabling integration with various spacecraft.
14. Next Steps
14.1. Detailed Design and Simulation
-
Feasibility Studies: Engage with aerospace engineers and scientists to conduct detailed analyses of the proposed design.
-
Engineering Studies: Initiate comprehensive engineering analyses to refine the rotating habitat ring design, focusing on mechanical systems, structural integrity, and human factors.
-
Simulation Modeling: Develop detailed 3D models and conduct simulations to test rotational dynamics, stress distribution, and crew acclimation to artificial gravity environments.
14.2. Collaborative Development
-
Partnerships: Collaborate with aerospace agencies, private space companies, and academic institutions to leverage expertise and resources.
-
Expert Consultations: Engage with specialists in human spaceflight, space medicine, and mechanical engineering to validate concepts and integrate best practices.
-
Partnerships and Collaboration: Foster relationships with space agencies, private companies, and academic institutions to pool resources and expertise.
-
Technology Development: Invest in R&D for the critical technologies required, such as advanced docking systems and AI guidance.
14.3. Prototyping and Testing
-
Scale Models: Build physical or virtual scale models of the rotating habitats to assess feasibility and identify potential issues.
-
Component Testing: Test critical mechanical components, such as bearings and seals, under simulated space conditions to ensure reliability.
-
Prototyping and Testing: Build scale models or simulations to test key components and systems, refining the design based on findings.
14.4. Risk Assessment and Mitigation
-
Failure Mode Analysis: Conduct thorough risk assessments to identify potential failure modes and develop contingency plans.
-
Safety Protocol Development: Establish comprehensive safety protocols and emergency procedures for crew protection.
14.5. Regulatory Compliance and Standards
-
Industry Standards: Ensure that the design complies with international space safety standards and guidelines.
-
Certification Processes: Plan for the necessary certification and approval processes required for human-rated spacecraft components.
15. Conclusion
16. Final Thoughts
Title:“Starship | Second Flight Test” https://youtu.be/C3iHAgwIYtI?feature=shared
@sisisimon “Wow stunning and amazing photos SpaceX!! I love them!!” https://x.com/sisisimon/status/1839445497888616898
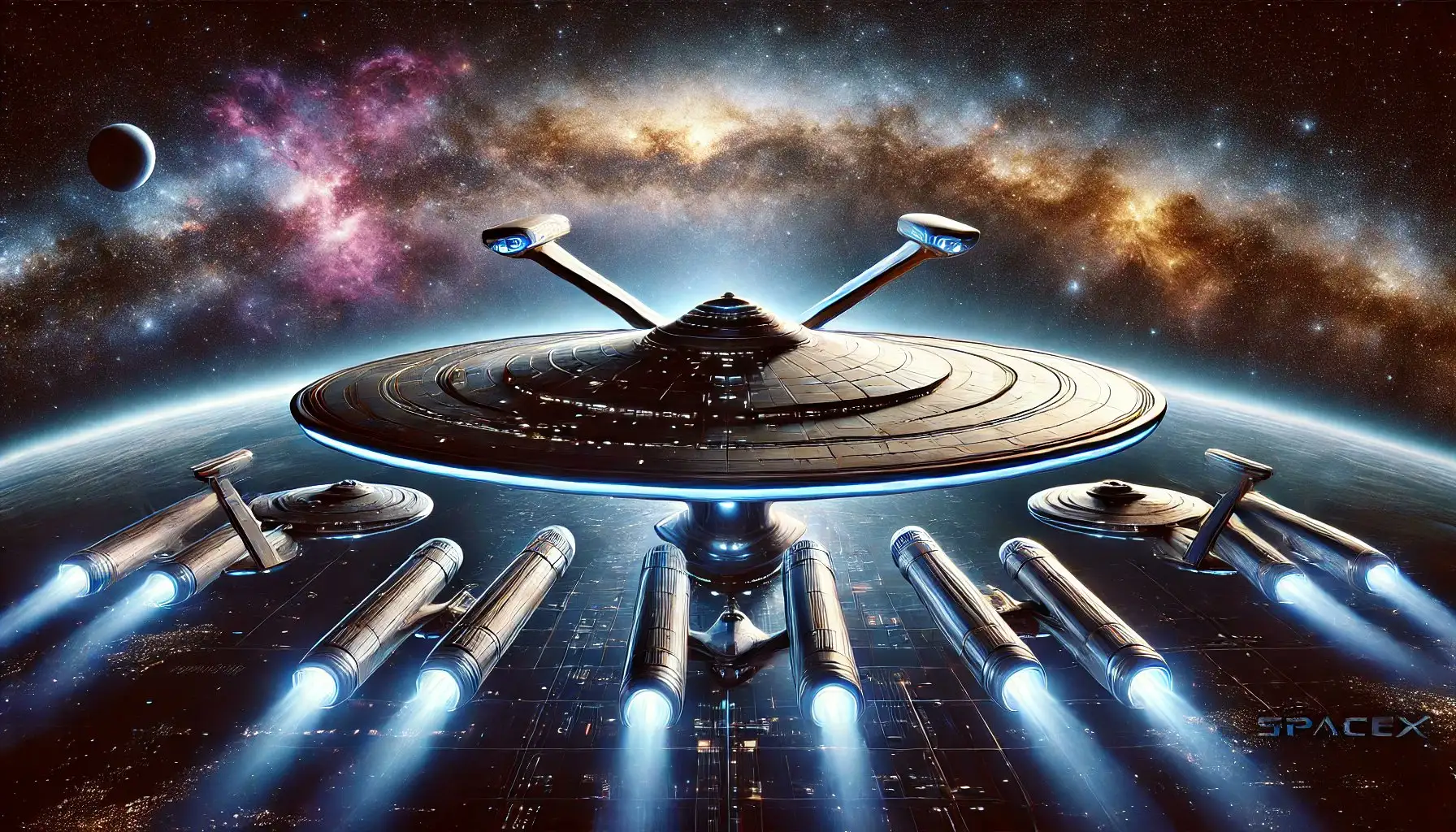
Related Content:
Title: “Creating Worlds: How the Genesis Sphere Brings Life to Star Systems” https://x.com/SkillsGapTrain/status/1845170029526175749
Title: “Engineering the Moon into a New Earth: A Positive Tech Vision for Sustainable Space Colonization and Engineering The Next Generation” https://skillsgaptrainer.com/engineering-the-moon-into-a-new-earth/
Title: @cb_doge “it’s fascinating how you’ve connected the numbers 69 and 420 to significant moments in Elon’s journey!” https://x.com/SkillsGapTrain/status/1845126500569223329
Title: “The USS Enterprise (NCC-1701-E) is better than money. And is better than gold or bitcoin as well.” https://x.com/SkillsGapTrain/status/1793914232108470515
Title: “Charting the Course: Realigning the AI Safety Board for a Future Forged in Innovation and Exploration” https://skillsgaptrainer.com/charting-the-course-realigning-the-ai-safety-board/
Title: “Masters of the Skies and the Digital Frontier: Commanding the Integration of Skills Gap Trainer Intelligence into U.S. Air Force and Space Command AI Systems” https://x.com/SkillsGapTrain/status/1802888099795780044
Title: “The Twin Flames of Prometheus: Elon Musk and Skills Gap Trainer, Igniting a New Era of Human Potential” https://x.com/SkillsGapTrain/status/1802469194790834568
Title: “Echoes of the Past: The Best of Two Worlds” https://skillsgaptrainer.com/echoes-of-the-past-the-best-of-two-worlds/
Title: “Interstellar Main Theme – Extra Extended – Soundtrack by Hans Zimmer” https://youtu.be/UDVtMYqUAyw?feature=shared
Title: “If you were on the Moon today, perhaps in a lunar base running out of oxygen and depressurizing, and you found yourself in Elon’s classic car collection” https://x.com/SkillsGapTrain/status/1828371122737357096
Web Location: https://skillsgaptrainer.com
To see our Donate Page, click https://skillsgaptrainer.com/donate
To see our Instagram Channel, click https://www.instagram.com/skillsgaptrainer/
To see some of our Udemy Courses, click SGT Udemy Page
To see our YouTube Channel, click https://www.youtube.com/@skillsgaptrainer